Cleanroom Air System Explosion
A significant system failure is the last thing a facilities supervisor needs during his first week on the job. Unfortunately, that is precisely what happened to Scott Sylvester at Organogenesis when he received word that the class 100 cleanroom air cooling system was down.
Organogenesis is a regenerative medicine company focused on developing and manufacturing products for the wound care and surgical and sports medicine markets. They must manufacture their products in cleanrooms, sterile environments designed to reduce the risk of product contamination.
Cleanrooms are controlled spaces where the concentration of airborne particles is kept within specified limits according to a classification and based on the cleanroom’s purpose. A class 100 cleanroom is a space that has 100 particles per cubic foot. For comparison, a typical office has between 500,000 and 1 million particles per cubic foot.
The CWM-8 chilled water unit provides the space with cooling and the necessary air changes required for the class 100 cleanroom designation. So, when the giant fan exploded right out of its housing structure, the cleanroom was shut down, and Scott was under severe pressure to get things up and running. The system was serviceable, but the fan suffered an enormous crack and had to be replaced.
Preparation
Identifying a viable replacement fan was more of a challenge than anyone would have anticipated. The CWM-8 chilled water unit location was in the back of a mezzanine, and the highly confined hallway leading to it only had 17” of clearance.
The team recommended replacing the large, damaged fan with four narrow fans to solve the problem.
LCA ordered the new fans, and the demolition crew disassembled the giant fan to remove it from the cramped mezzanine and make room for the replacements.
Installation
Two electricians, two LCA installers, and the LCA project engineer were onsite for the day of installation. While the Organogenesis team had to perform cleanroom tests before turning it over to manufacturing, LCA completed the entire project from diagnosis and complications to delivery and installation within ten days.
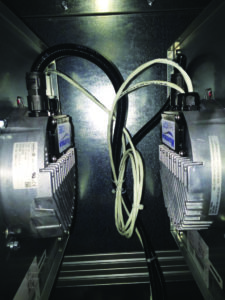
“My first thought was how are we going to get a new housing up here,” stated Scott Sylvester, Organogenesis facilities supervisor. “We called LC Anderson thinking a major construction project would be needed, including roof penetrations to pull this job off. However, I was relieved at their proposed solution and for making it all happen in a timely manner. Overall, it was a great solution to mitigate downtime for our most critical space.” The facilities supervisor went on to say, “Not only were the fans smaller dimensionally, but their lack of maintenance was also a huge bonus. In addition, the new variable speed ECM fans are a huge help when balancing the laminar flow in an ISO 5 cleanroom.”
The Manager of Calibration & Maintenance at Organogenesis sent an email to everyone involved expressing his appreciation. “Thank you to Scott S; great 1st week on the job, for spearheading the project. Our great HVAC service team at LC Anderson jumped through hoops to make the repair happen. A project and repair that seemed daunting and impossible completed seamlessly in under three weeks.”
Organogenesis’ Assistant Vice President of Manufacturing Operations had this to say, “Thank you to everyone – this particular repair is very impactful (in a positive way) to manufacturing in light of higher production builds.”